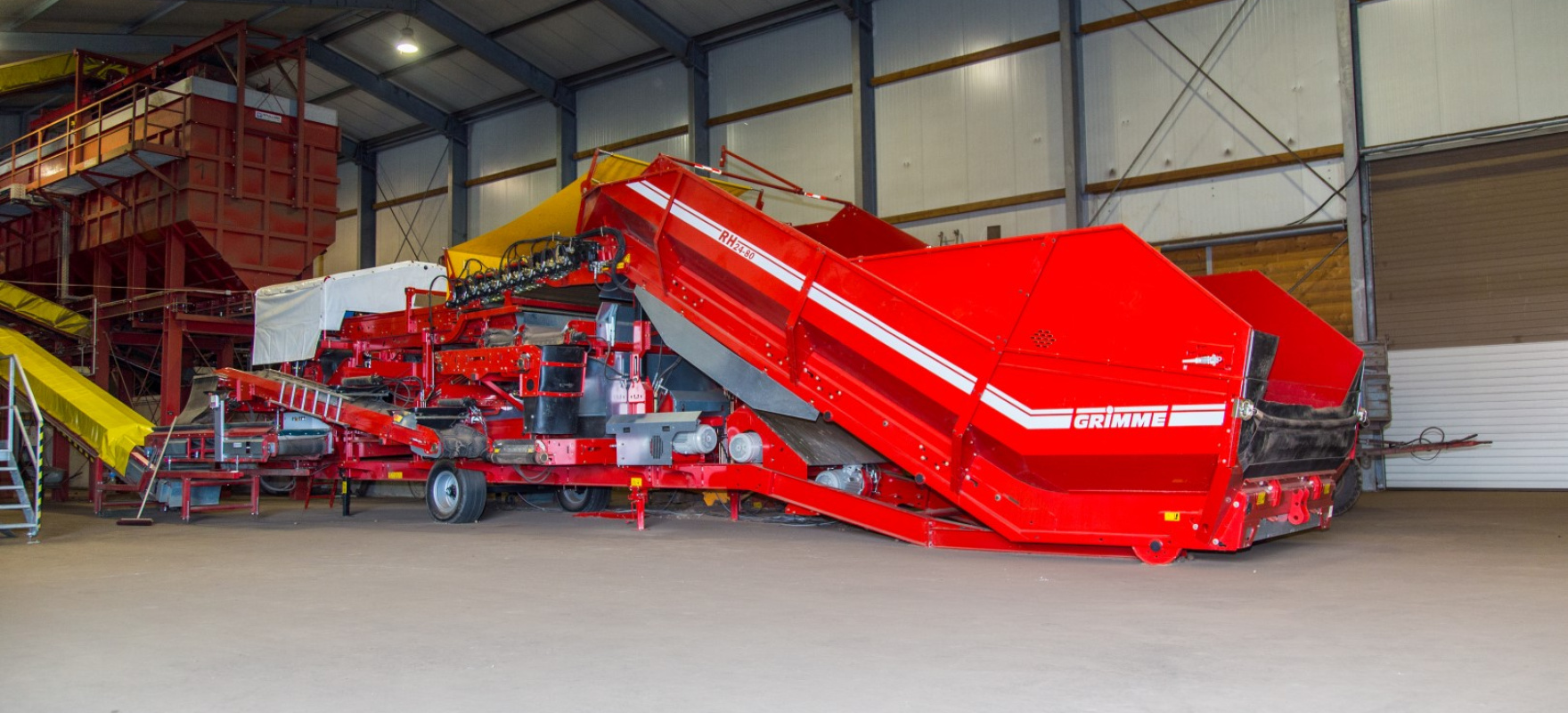
PowerCombi
UP TO 25% IMPROVED STORAGE CAPACITY
Customers who want to achieve maximum utilisation of their storage capacity use both receiving hopper with combined separation technology and picking tables, in
Customers who want to achieve maximum utilisation of their storage capacity use both receiving hopper with combined separation technology and picking tables, in order to effectively separate the potatoes from soil, stones, clods and weeds. The maximum capacity of such systems is around 80 t per hour. Due to technological advances in harvesting equipment and logistics the demand for more efficient and cost effective inspection systems has also increased.
With the launch of the PowerCombi, GRIMME is able to use a 26 - 28 m³ receiving hopper with three highly efficient separation mechanisms to not only increase separation accuracy, but also increase capacity up to 100 tonnes per hour. Up to 25% more efficient than the previous system!
The first separator is comprised of three infinitely adjustable rollers made out of the highly durable plastic polyurethan, which helps to separate loose soil, breaks up lumps of soil as well as separating smaller, waste potatoes. The second separator is made of two specially designed rotating rollers, to aid further with separating smaller potatoes from the main crop.
The desired crop, oversized potatoes and other remaining impurities then pass through to the third separating device. This removes lumps, stones and other waste products through the optical high performance separator, called FPS (Field Potato Sorter), built by the specialist company Tomra. The FPS scans all items "on the fly" with an infrared sensor and recognized lumps, stones and other unwanted wastage and throws them out with small fingers. The potatoes continue unharmed through the machine and onto the following conveyors.
In order to achieve such high levels of efficiency, the separation belt is 2.4 m wide in all units. The constant width without any bottleneck avoids damaging of the crop. An electro-mechanical sensor over the main product conveyor avoids the danger of the FPS getting damaged by items such as large stones or wood.
Due to the high and exact separation of the PowerCombi, operating at up to 98% efficiency, far less staff are required to check for waste products and therefore this allows for considerably lower labour costs. In theory this system could replace up to eight employees. The PowerCombi can easily be operated by a sole person.
The result is up to 25% greater efficiency compared to other systems as well as a superior separation system. A higher proportion of sellable goods in the sheds increase the yields, leading to both lower storage costs as well as better air circulation.
Video PowerCombi
Innovation
Whether its new machines or digital solutions, you'll find all the latest information here.
Display all updates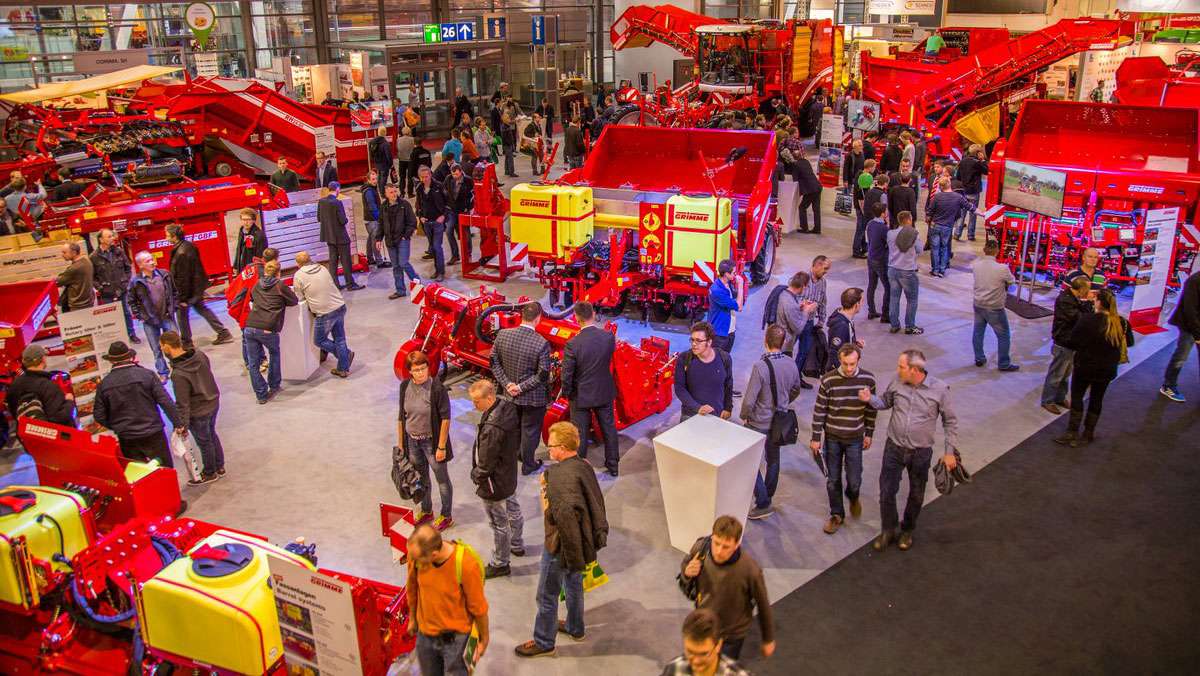